CARBON FIBER PRODUCT STUDIES
The use of carbon fiber dates back to the 1950s and has evolved over time to revolutionize many industries.
1. Initial Discovery and Development (1950s - 1960s)
The first production of carbon fiber was made by Sir Roger Bacon. Bacon initiated the early research of carbon fiber. In the 1960s, the potential of carbon fiber began to be understood by some companies. During this period, carbon fiber was generally investigated for use in military applications, especially in aircraft and rockets.
2. Beginning of Industrial Applications (1970s)
In 1971, Toray Industries (Japan) took an important step for the commercial production of carbon fiber. At that time, it was considered an important development in the search for high-performance composite materials. In the 1970s, the industrial use of carbon fiber began to expand. In particular, the aviation and aerospace industries began to use carbon fiber for lightweight and strong structural components. The most well-known applications of carbon fiber during this period include aircraft wings and rocket parts.
3. Developing Technologies and Popularization (1980s - 1990s)
In the 1980s, carbon fiber production techniques were developed. The development of Pan (Polyacrylonitrile) based carbon fiber enabled the production of high-performance carbon fiber at lower costs. During this period, carbon fiber began to be used in areas such as automotive, sports equipment and construction. In the 1990s, the widespread use of carbon fiber increased in areas such as the automotive industry and the bicycle industry. Carbon fiber began to be used in automobiles and sports vehicles that require high performance thanks to its lightness and durability. In addition, research was conducted in other industries such as medical devices and electronics.
4. Today
In the 2000s, carbon fiber became more widely used in the automotive industry. Carbon fiber parts were used especially in high-performance car models. In addition, aircraft manufacturers and space agencies continued to use carbon fiber more. In the 2010s, electric vehicle manufacturers also used carbon fiber to increase energy efficiency. The use of carbon fiber in motor sports such as Formula 1 has become more widespread to increase the speed and strength of vehicles. Carbon fiber has a structure that is bundled in the form of thin wires in micron size (8-10 microns) and is usually combined with polymer resins to become a composite material. In this way, it provides superior mechanical properties to the final products. Known for its high durability, lightness and high strength, carbon fiber reinforced composite is preferred by engineers for manufacturing due to its high mechanical requirements.
Areas of Use of Carbon Fiber Reinforced Composites
- Space Technology
- Defense Industry and Aviation Sector
- Automotive Sector
- Maritime Sector
- Robot Technology
- Electrical-Electronic Technology
- Chemical Industry
- Medical Field (Manufacture of medical devices)
- Musical Instruments Industry
- Construction and Building Sector
- Sporting Equipment Manufacturing
It is used in areas such as.
Features That Make Carbon Fiber Reinforced Composite Preferred
Lightness
Carbon fiber is twice as light as aluminum and five times as light as steel. This helps reduce structural weight, providing advantages especially in transportation and fuel efficiency requirements.
High Durability and Strength
Carbon fiber is a material with high tensile strength, which means it is strong. It is ideal for many structural applications, minimizing the risk of deformation.
Chemical Resistance
Carbon fiber is extremely resistant to harsh chemical conditions such as acidic and alkaline environments. This feature allows it to be used in demanding areas such as industrial machinery and marine.
Thermal Resistance
Carbon fiber is resistant to high temperatures and can withstand up to 2000 °C. However, this temperature range may vary depending on the type of resin used.
Electrical Conductivity
Carbon fiber exhibits electrical conductivity. This feature is especially advantageous in some electronic and electrical applications, while also serving to block electromagnetic leakage.
High Modulus
The modulus (modulus of elasticity) of carbon fiber makes it an excellent structural material. A high modulus indicates that the material has a low amount of stretch.
Corrosion Resistance
Compared to metal materials, carbon fiber does not rust or corrode. This is a great advantage, especially for applications exposed to water, salt or other corrosive substances.
Low Thermal Expansion
Carbon fiber shows minimal increase in size change due to temperature changes. This feature is important in precision engineering and aerospace applications.
Aesthetics and Visuality
Carbon fiber is used as a design element in the automotive and bicycle industries due to its aesthetic appearance.
Machinability and Manufacturing Challenges
Carbon fiber reinforced com Posit is known to be a difficult material to produce and process. However, with modern production methods, it can be produced and processed quite efficiently.
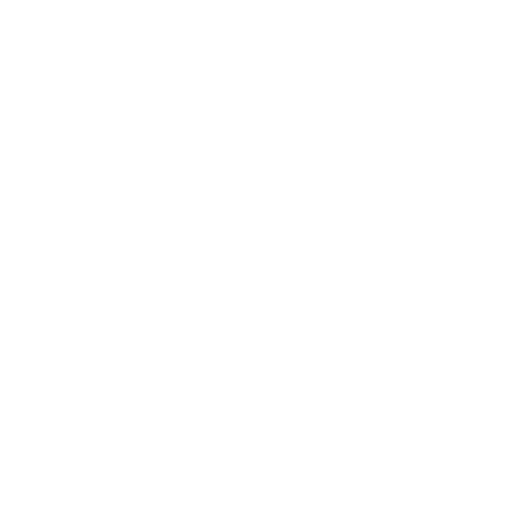
Bu sitede kullanıcı deneyimini geliştirmek ve sitenin verimli çalışmasını sağlamak için çerezler kullanılmaktadır. Daha fazla bilgi için Çerez Politikamızı okuyun.
OK